
Hydraulic HVAC/Copper Cold Weld Sealing Hand Tools
Download our Hydraulic Tool Series PDF
Producing quick, airtight bonds, Simond’s Hydraulic crimping tools are like no other.
Air-driven Hydraulic Pump, HYP-24
Like no other.
Simonds Hydraulic crimping outfits produce a bilateral seal in ductile metal tubing by symmetrically collapsing, cold welding, and severing tubulation with no loss of vacuum or pressure.
Hand guided.
One step Crimp/Seal
Used in air conditioner, refrigeration, HVAC, and laser tubing markets
Produces quick, air-tight bonds in OFHC copper tubing (or equal).
Precision carbide pinch-off rollers provide clean, dependable, cold-welded hermetic seal.
Choose from:
Product # | Tubing Diameter (x0.35" wall) | Elongation (per side) |
Flare (razor edge) |
Distortion (min. stub length) |
---|---|---|---|---|
HY-125 | 1/8" | 0.50" (1/8") | 0.170" | 0.125" |
HY-187 | 3/16" | 0.50" (1/8") | 0.250" | 0.187" |
HY-250 | 1/4" | 0.50" (1/8") | 0.350" | 0.250" |
HY-500 | 1/2" | 0.55" (3/16") | 0.750" | 0.500" |
HY-750 | 3/4" | 0.375" (3/8") | 1.150" | 0.750" |
HY-1.0 | 1.0" | 0.50" (1/2") | 1.50" | 1.0" |
The chart shows typical tube deformation of the Simonds standard outfit's. Simonds has been a leader in developing more specific tools to meet the demands of the production line. Quotations for specialty tools are available on request.
Copper cold weld cutter in action.
In this video you can clearly see the jaws closing when the hydraulic pump is activated. The copper is crimped between the rollers in the jaws and the excess "pops" off. You can see that there is a razor thin crimp in the tubing giving a mechanical, permanent vacuum seal.
Using the Simonds hydraulic tool eliminates the need to weld a tubing crimp. This step elimination will speed up production, form a more positive crimp and increase production. Simonds standard Hydraulic tools will crimp up to 1/2" soft tubing. We have designed and manufactured tools for crimping up to 3/4" tubing and crimping exhaust pipes together.
We excel at tweaking our off-the-shelf products into a custom solution based on your needs.
In this custom tool image above, our engineers created a tool with rollers working in parallel instead of a typical arc travel.
Interested in seeing what Simonds can do for your project? Check out our Custom page here:
Our hydraulic cold weld product excels with these elements. From Copper, Nickel, Iron, Silver, Gold and Aluminum.
Cold Welding Information
TUBULATION SELECTION
The most commonly used metal for pinch-off is OFHC Copper (ASTM B68-83, B75-84, B133-83 and B170-82). This has the specifications, chemistry and state of ductility for billet-certified 99.99% pinch off grade copper. It is important that the material be bright annealed at 650° C to 850° C for 30 minutes in a dry hydrogen atmosphere. This is required because the material will undergo a deformation of approximately 350% during pinch-off. High-Purity nickel ( A Nickel, NI270, NI200 or 99.4% nickel ASTM-B161) is another commonly used material. High-purity nickel offers several advantages: minimal out gassing during bake out and pinch-off, minimal oxidation and higher temperature bake ability.
Nickel tubulation must be fully annealed at 1150° C for 30 minutes before pinch-off. Good results can also be obtained using aluminum (annealed 3003 H14, 98% classified non-heat treatable), pure iron, gold, platinum, silver and columbium.
The cold welded area will be work hardened during the pinch-off. The size and length of the cold welded area will depend on material, type of annealing, cleanliness, wall thickness and radius of the pinch-off anvil inserts.
PINCH -OFF PREPARATION
The tubular material being used must be totally free of contamination at the weld point. Mechanical or sonic cleaning rather than chemical cleaning just prior to pinch-off yields the best cold welds. The O.D. of the tubing should be polished with 320-grit emery cloth to remove oxide crystals.
The tungsten carbide inserts of the tools jaws must be cleaned before each pinch-off. Any contamination pressed into the metal at the weld point can injure the cold-welded seal. The pinch-off is a cold extrusion and a lubricant can be used to aid the material flow. Clean #10 machine oil works well on most metals.
During the pinch-off, pressure must be applied evenly until the tubing severs suddenly. Any interruption of this process while the material is in a plastic state will result in an incomplete cold weld. Leaks are apt to occur if the pinch-off phase is incomplete and the tubing needs to be wiggled apart. The HY-187 Hydraulic outfit provides reliable service and assures the best results.
AFTER PINCH-OFF
There are a few methods for checking the finished crimp for leakage.
Vacuum insulation time rates and electric resistance measurements can be avoided if a sample tube is carried through the entire process, then subjected to a helium test or microscopic examination, using the sample for comparative analysis. Process procedures should be duplicated precisely, changes as subtle as bending a piece of copper tubing will change its grain structure and work-harden the piece considerably. There could be significant changes in grain size, crystal structure and ductility during any thermal process such as brazing, bake-out, soldiering or welding.
The cold-welded stub should be protected with a plastic cap after pinchoff, as it is a delicate seal and very sharp.
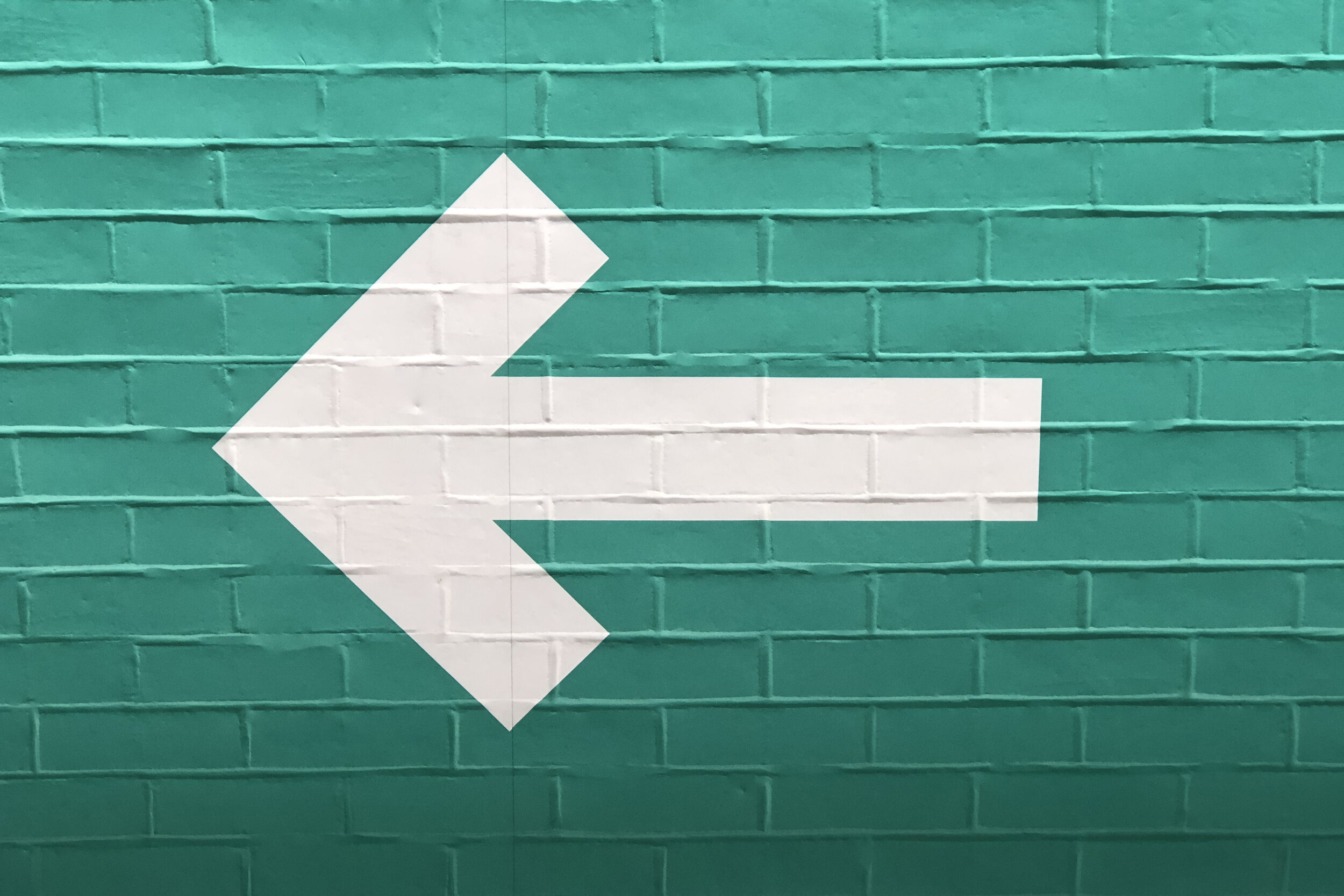
Find out more info about this tool here.
From pricing, to stock availability to options that can make your workstation super-easy and efficient.